Passivation Plant reduces lead time for spring and bent wire forming
11 February 2013
William Hughes has installed a NADCAP and Honeywell approved Passivation Plant at its UK HQ in Stalbridge, Dorset.
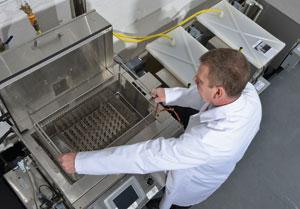
“The decision to start thinking about passivation came about because one of our significant aerospace customers ceased this activity,” explains Special Processes Manager, Shaun Tattershall. “As a result we began investigating various plant options and initiated a request for processing approval from our major aerospace customer.”
Mr Tattershall was successful in sourcing machinery that was designed and manufactured to William Hughes’ precise requirements and offered optimised control of the process in line with AMS 2700.
“This helped with our forward plan of gaining a Chemical Processing Nadcap accreditation,” he says. “We have also achieved Honeywell approval for passivation, and we appear on their approved processing supplier list.”
Representing a substantial investment, the new passivation plant at William Hughes offers novel functionality in that there is no manual ‘dunking’ of component baskets from station-to-station, as with traditional systems. Instead, the plant performs ‘fluid transfer’, moving chemical solutions from holding tanks into the main processing unit as required. The entire process is automatic and PLC controlled. Typical treatments are nitric acid/sodium dichromate, and rinse cycles. These are followed by a final rinse in deionised water before a drying cycle.
Other innovative plant functionality includes an ultrasonic passivation facility and a rotary option where parts can be rotated through the solution, thus filling air gaps in more complex and tubular-type components, for example.
“William Hughes has invested in training and professional advice for passivation, particularly from a control point of view,” states Mr Tattershall. “For instance, we have to ensure that the tank solutions are controlled to the required specification tolerances at all times. We perform weekly checks in our laboratory to ensure these are correct, along with checking other factors such as pH and conductivity.”
Some checks are performed using intelligent machine functions. For instance, the PLC-controlled passivation plant at William Hughes will monitor and automatically adjust pH levels in the rinse water, as well as police conductivity in the final processing deionised water tank.
“Ultimately the service will be offered to all customers – not just those in the aerospace sector – on a subcontract basis,” concludes Mr Tattershall. “There will be three service levels: standard five-day; express three-day; and super express 24 hours [subject to any testing requirements]. All services are designed to focus on the customer for high quality and fast turnaround. The working envelope size available is 520 x 300 x 200 mm.”
Since installing the passivation plant, William Hughes has relocated its Nadcap-accredited heat treatment and ultrasonic cleaning equipment into the same area, thus creating a brand new process department.
Other Press Releases By This Company
- 30/08/2023 - Significant investment keeps automotive supply chain agile and just-in-time
- 27/04/2023 - Over-moulded Lumbar Structure
- 10/01/2023 - Technology investment boosts cleanroom capabilities at William Hughes
- 09/06/2022 - William Hughes is welded to success
- 13/01/2022 - New tech, new capacity & new capabilities at William Hughes
- 09/08/2021 - Insulated bus bars formed without coating damage thanks to new approach to bending
- 03/12/2020 - William Hughes goes solar with Low Carbon Dorset - saving energy costs and reducing its carbon footprint
- 12/08/2020 - Springing into action saves the day for automotive tier one
- 19/12/2019 - William Hughes boxes clever with spot welded assembly for storage tray
- 19/11/2019 - Test Point Beads Provide a Fast and Flexible Way to Insulate and Support Components on Printed Circuit Boards
- 13/08/2019 - William Hughes can now offer Electrophoretic Painting for the protection for metal parts
- 08/07/2019 - William Hughes introduces metrology services for high precision manufacturing following the acquisition of JK Metrology
- 14/03/2019 - Salt spray testing keeps a check on corrosion-resistance at William Hughes
- 25/10/2018 - Secondary processes and finishes for springs and wire components
- 27/09/2018 - Passivation explained and demonstrated
- 31/05/2018 - William Hughes uses testing to guarantee components meet endurance requirements
- 12/12/2017 - William Hughes vacuum formed trays help protect valuable parts during storage and transportation
- 11/10/2017 - William Hughes expands European operations with the acquisition of Nosag Polska Sp. z o.o. from the DEFTA Group
- 14/09/2017 - William Hughes meets new challenges for high performance spring in critical aerospace application
- 07/08/2017 - William Hughes takes the stress out of spring specification
- 22/03/2017 - Critical components cleaned to the most demanding quality standards, approvals and specifications
- 17/02/2017 - Ultrasonic cleaning comes to Southern Manufacturing & Electronics
- 13/12/2016 - William Hughes shares spring making secrets on youtube
- 12/10/2016 - William Hughes invests £1/4 million in latest welding technology to meet growing demand for automotive seat frames
- 29/06/2016 - William Hughes apprentice programme provides young people with engineering career opportunities
- 06/06/2016 - Latest 3D measurement scanner from William Hughes
- 18/02/2016 - Clean bill of health for William Hughes
- 18/01/2016 - Specialist springs from William Hughes help improve car comfort and safety
- 11/04/2014 - William Hughes celebrates 10 years of success in Bulgaria
- 21/01/2014 - William Hughes is sole supplier of specialist compression springs to Eaton Fluid Power in Havant
- 25/10/2013 - William Hughes adds strength and versatility to its wire components with new overmoulding capability
- 16/09/2013 - Coiled and ready for action
- 08/08/2013 - Wire-form & Spring specialist expands services portfolio
- 28/06/2013 - William Hughes continues to grow its manufacturing facilities in Bulgaria
- 30/01/2013 - Plasma Welding expertise at William Hughes
- 18/01/2013 - Bent Wire from William Hughes gets you on the move
- 20/12/2012 - William Hughes Spring Technology at the heart of Deltex Blood Flow Monitor
- 07/12/2012 - Speedy wire solution to rear car seat frame challenge
- 02/11/2012 - Improved Spiral Springs from William Hughes
- 05/09/2012 - Need double torsion springs? No problem for William Hughes
- 03/09/2012 - William Hughes achieves NADCAP accreditation
- 16/07/2012 - Hughes expands Compression and Torsion Spring ranges