Priorclave advises on Autoclave replacement
04 August 2009
Most laboratory autoclaves spend their lives hidden away in the corner of lab and are only noticed if they stop working.
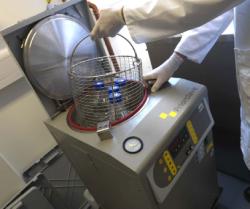
When it is time to replace or upgrade your autoclave however, you should take time to consider your options. The working life of an autoclave is upwards of 5 years and with the capital expenditure involved you may not be able to replace what you have chosen for some time to come. The following are a few suggested steps to take to ensure that your next autoclave is as forgettable as possible.
Step 1: Look at what you have already.
Is it big enough for what you do now and what you might do in the future? Would a front loading model be more convenient than a top loader and if so, have you got room for one? How many cycles do you need to get through in a day? Does it do what it needs to do? A large range of options and accessories are available including vacuum systems and flashy control displays. Do you need these and will your staff be able to operate them? Remember that the more complex something is the more things there are to go wrong with it.
Step 2: Discuss it with the people who will use the autoclave and find out what they want.
An operator who feels left out of the specifying process can often be the cause of many unnecessary service visits and ‘faults’. Also discuss with the Finance Department how big the budget will be. Some manufacturers’ options and accessories are easily fitted to the autoclave at a later date, so if there is not quite enough budget for all that you want, you can still upgrade inexpensively at a later date.
Step 3: Put together a written specification. This will help suppliers to offer the right equipment and help you to check that they have supplied you with what you want. You should ask suppliers to tell you how their autoclave meets your specification or otherwise.
Step 4: Get prices from manufacturers or their distributors. When comparing prices take time to look at what is included in the price so that you can be sure you are making a valid comparison and that you don’t end up buying the cheapest offer and finding it does not do what you thought it would do. Make sure that the supplier is offering what you want and not what they think you want. Any reputable supplier will be able to provide assistance, advice and information on these questions and often you will be able to arrange a site survey to make sure that everything is going to fit.
Step 4: What happens after the autoclave is delivered? On-going maintenance and service should be considered as part of the purchasing process, after all, you would not buy a new car and expect it to run forever without servicing. Make sure that you do not save a few pounds on the initial purchase only to end up with inconvenient ‘down time’ afterwards. Find out whether preventative maintenance is available and what is covered by different suppliers’ preventative maintenance packages and warranties. Also determine how well they perform in terms of call out times and ability to fix the equipment when they arrive.
Step 5: Place your order. In the end it is your choice. Of course price is an important factor but sound research and reliable backup to ensure trouble-free installation and operation may very soon turn out to be a wise investment too.
Other Press Releases By This Company
- 14/06/2023 - Priorclave Shows New Autoclave Ranges at Analytica Lab Africa
- 25/01/2023 - New Autoclaves, Easier Match
- 11/08/2022 - High-Throughput Autoclave Cuts Sterilisation Costs
- 26/11/2020 - ACT Gives Priorclave Green Credentials
- 04/06/2020 - Priorclave gains Saudi Arabian FDA Approval for its Autoclave range
- 06/02/2020 - Priorclave Launches Global Autoclave Website
- 17/01/2020 - Priorclave Shows Autoclave Range at Medlab 2020
- 14/11/2019 - Lab Autoclaves with Eco credentials at Medica 2019
- 19/06/2019 - Priorclave Extends its Sterilising Support to Laboratories
- 24/05/2019 - Priorclave Launches New Autoclave Controller
- 25/01/2019 - Priorclave Shows Latest Autoclave Advances at Medlab 2019
- 15/10/2018 - Priorclave Launches New Autoclave Developments at Medica 2018
- 09/08/2018 - Priorclave’s Autoclaves NOW Have Wi-Fi Connectivity
- 27/03/2018 - Examine Priorclave's latest autoclave functionality at ACHEMA
- 07/03/2018 - Autoclaves renowned for reliability at Analytica 2018
- 06/03/2018 - Priorclave celebrates 30 years manufacturing Autoclaves
- 22/02/2018 - Priorclave Draws in Visitors at Medlab exhibition
- 16/01/2018 - Priorclave Highlights Versatile Front-loading Autoclave at Medlab
- 09/11/2017 - Priorclave Energy Efficient Autoclaves at Medica
- 02/11/2017 - Priorclave Wins Prestigious US Autoclave Contract
- 02/08/2017 - Printer Up-Grade on Lab Autoclaves
- 05/07/2017 - Priorclave Appoints New CEO for its American Operation
- 15/05/2017 - Compact Top Loading Autoclave for Labs with Limited Space
- 24/03/2017 - 25th Anniversary for Priorclave’s Service Manager
- 03/02/2017 - Stackable Autoclaves from Priorclave give Labs Greater Sterilising Flexibility.
- 25/01/2017 - Energy Efficient Lab Autoclaves featured at Medlab
- 11/11/2016 - Priorclave launches an autoclave How to Build video
- 10/10/2016 - Priorclave Features Energy Efficient Autoclaves at Medica
- 16/09/2016 - Priorclave Appoints New Service Manager
- 02/09/2016 - Priorclave Launches New 400 Litre Autoclave
- 25/07/2016 - Autoclave Manufacture Launches New Top Loader
- 08/07/2016 - Priorclave Signs up to London Living Wage
- 16/06/2016 - Priorclave Awarded £½M Autoclave Export Contract
- 21/04/2016 - Higher Throughput, Lower Cost Lab Autoclaves
- 18/11/2015 - Free impartial guide to Autoclave selection
- 09/11/2015 - New Faces in Priorclave’s Customer Care Team
- 22/10/2015 - Priorclave Reveals the Inside Story at Medica – stand 1EO2
- 08/09/2015 - Cylindrical Camber Autoclave Breaks the Rules
- 07/07/2015 - New Autoclave Designed for Sterilising Extra-bulky Dense Waste
- 01/05/2015 - Tamperproof Laboratory Autoclaves
- 12/02/2015 - Priorclave Features Top Loading Autoclaves at Arab Health
- 05/12/2014 - New Autoclave Product Guide from Priorclave
- 19/09/2014 - Bigger Capacity Benchtop Autoclave meets customer wish list
- 19/08/2014 - Priorclave RCS Autoclaves improve Laboratory efficiency
- 22/07/2014 - Small Vacuum Autoclave perfect for sterilising difficult items
- 11/07/2014 - Latest Compact Top Loading Autoclave from Priorcvlave
- 04/07/2014 - Sterilise short and tall items side-by-side
- 28/05/2014 - Get an insight into Britain’s best innovative Autoclave manufacturers
- 01/05/2014 - Priorclave launches range of Autoclave consumables
- 14/04/2014 - Cylindrical Autoclaves Improve Lab Performance
- 11/11/2013 - Priorclave Launches Largest Round Chamber Autoclave
- 17/09/2013 - Autoclaves for start-up laboratories
- 15/08/2013 - PowerDoor Autoclaves for small Laboratories with big requirements
- 05/07/2013 - Large Chamber Laboratory Autoclaves for bulky items
- 30/05/2013 - Proven Autoclave design is a long runner
- 16/05/2013 - Priorclave set to target North American lab market
- 18/04/2013 - Priorclave appoint new Sales Director
- 14/03/2013 - Britain’s most successful Autoclave manufacturer celebrates 25 years
- 04/02/2013 - Priorclave simplifies loading of Vertical Autoclaves
- 30/07/2012 - Priorclave launch Autoclave Performance Analyser
- 16/07/2012 - Priorclave appoint new Sales Manager
- 16/07/2012 - Priorclave secure further Autocalve export contracts
- 03/05/2012 - Priorclave to unveil Autoclaves with touch screen controls at Achema 2012
- 17/04/2012 - Priorclave incentive for steamy affair
- 10/04/2012 - Priorclave cuts sterilisation costs at York University
- 20/03/2012 - Priorclave supplies Autoclaves to new academic health science centre facility
- 23/01/2012 - Priorclave leg mounted Autoclaves for designated Clean-Rooms
- 19/12/2011 - University lab invests with Priorclave for better performance
- 16/12/2011 - Priorclave success at London Vet Show
- 11/11/2011 - Priorclave to feature design flexibility at Medica
- 11/10/2011 - Into Africa - Priorclave Autoclaves in eary shipment
- 21/06/2011 - Priorclave meet specification 'head on' with Benchtop Autoclave
- 20/05/2011 - Science World to show latest Compact Autoclaves from Priorclave are small by design but big on features
- 21/04/2011 - New Priorclave Autoclave bound to be first
- 24/02/2011 - Priorclaves' healthy return from Medlab exhibition
- 06/12/2010 - Priorclave take a stand at Arab Health Exhibition
- 24/03/2010 - Priorclave combats surface microbial growth
- 04/12/2009 - Priorclave at Arablab 2010
- 18/09/2009 - Walk into Priorclaves' Autoclave at Medica 2009
- 24/08/2009 - Autoclave positioning and installation- some tips from Priorclave
- 20/08/2009 - Planning a Double-Door Autoclave for clean rooms or containment suites
- 07/08/2009 - Keeping pace with Autoclave technology
- 06/08/2009 - Priorclave offers help choosing Laboratory Autoclaves
- 05/08/2009 - Why bother with calibration and performance qualification testing of Autoclaves.
- 26/06/2009 - Priorclave Autoclaves at your service
- 16/04/2009 - Priorclave makes a stand at Achema