Intelligent Extruder plans its' own growth
12 September 2007
A bench top extruder developed at Bradford University is able to collect data about its own operation and to determine a wide range of characteristics of the material with which it is working.
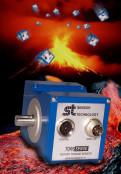
Most of the intelligence is provided via a digital TorqSense torque sensor, which uniquely collects data via a radio signal rather than being hard wired to the extruder, and passes it onto a computer for analysis.
The extruder, developed under a commercial contract by Dr Raj Patel, supervised by Professor Hadj Benkreira, is specifically for use with fine chemicals, as used in industries such as electronics, plastics, nanotechnology and pharmaceuticals.
One element of the design brief was that it should be easy to scale up to create full sized production extruders. Dr Patel explains: "This requirement immediately made me think of using a TorqSense. Comprehensive mapping of torque requirement and how it varies at different speed and with different materials allows us to quickly define the power train that will be required on production-scale machines."
He had used TorqSense on earlier projects, and particularly liked the fact that it was a digital system with digital outputs and the lack of hard wiring and slip rings made resetting the extruder between the many test runs far simpler and quicker. "As well as developing the extruder design, we are charged with developing new materials. For instance the semiconductor industry adds conductive carbon to silicon to make silicon wafer substrates.
Each such recipe has different mixing and extruding characteristics, which we are measuring. "Significantly the end users often need to optimise certain characteristics of their materials, such as elasticity or conductivity. Surprisingly many of these can be measured directly through the TorqSense because they have a proportional affect on the material's viscosity and therefore torque requirement." TorqSense torque transducers, available from Sensor Technology of Bicester, use two tiny ceramic piezoelectric frequency resonating combs otherwise called Surface Acoustic Wave (SAW) devices that are fixed onto the shaft of the torque sensor to measure applied torque.
As the torque changes the combs vary their spacing and consequently the resonant frequency of the SAWs changes proportionally to the torque applied in the rotating shaft. In effect the combs are frequency dependent strain gauges that measure changes in resonant frequency of the shaft. A wireless radio frequency (RF) coupling is used to interrogate the SAWs and transfer the data signal to a pick-up head.
The same RF coupling is used to supply power to the SAW devices and because the gauges are based on piezo technology they need less than one milliwatt of power. This arrangement does away completely with the difficulties of fitting slip rings and maintains the measurement quality throughout an extended test run. TorqSense embraces all the advantages of SAW technology, including no load imparted or extra drag to the drive mechanism under investigation.
As it is fundamentally a digital system it has a broader signal bandwidth than other analogue based technologies and electromagnetic interference is eliminated. This extruder project is a follow-on to earlier work on a mini-mixer for using in formulating high performance plastics, in which a TorqSense played a similar role.
The technologies that Dr Patel and his colleagues have developed will transfer directly to the plastic industry and other soft solid sectors giving rapidly recovery of the development costs. "The software we have developed to analyse the extruder’s performance and materials properties," says Dr Patel, "is now being restructured so that it runs on a PLC rather than a PC. As such it will be able to control production sized units in real-time, making them self-adjusting and ensuring perfect results every time."
Other Press Releases By This Company
- 11/03/2019 - Sensor Technology keeps hydraulic projects on course
- 14/01/2019 - Mass market electric vehicles getting revved up for launch
- 15/11/2018 - Measuring torque without slip rings
- 16/07/2018 - Pay as you sense
- 08/06/2018 - Long service motors tested after re-engineering
- 05/04/2018 - Optical rotary torque sensors suitable for low torque and high band width measurements
- 20/02/2018 - Pump and valve innovator finds a test rig technology that talks the torque
- 20/02/2018 - Electric vehicle pioneer favours wireless test rigs
- 05/02/2018 - Pump and valve innovator finds a test rig technology that talks the torque
- 14/12/2017 - Chemical engineers talk sense about mixer efficiencies
- 14/11/2017 - Sensor Technology keeps hydraulic projects on course
- 14/09/2017 - Electric vehicle pioneer favours wireless test rigs
- 21/06/2017 - Torque test ensures reliability of steerable drills
- 10/06/2013 - Torque Sensor guarntees Tip Top-Taps!
- 30/08/2012 - Automotive Innovations Torque Up Manufacturing Revival
- 31/07/2012 - Torque of a Motor Revolution
- 12/06/2012 - Torque test ensures reliability of steerable drills
- 30/04/2012 - Engineers Torque Technology To Medics
- 29/03/2012 - Long Service Motors Tested after Re-Engineering
- 01/02/2012 - Back Manufacturing, But That Is Only Half The Story
- 23/12/2011 - Pay as you Sense
- 02/11/2011 - New wave and tidal turbine concept promises clean, affordable energy
- 05/10/2011 - Ground Crews talk sense on Generator Maintenance
- 08/09/2011 - TorqSense transducers help to guarantee valve actuator performance
- 08/08/2011 - Company Profile
- 11/05/2011 - Sensing growth opportunities
- 25/03/2011 - Drama as Helicopter sensor flies into Theatre role
- 07/02/2011 - Technology transfer tests tree safety
- 18/01/2011 - Sensor Technology helps to keep sheep shorn
- 02/12/2010 - Smart Load Sensor
- 13/10/2010 - Novel sensors aid tidal turbine development
- 01/09/2010 - Torque Sensor helps reduce engine friction
- 12/08/2010 - Tidal Turbine to light the Thames
- 22/06/2010 - Sensor Technology Provides the Key to Learning
- 05/05/2010 - Talking Sense About Technology Transfer
- 16/04/2010 - ULTRASOUND HELPS OPTIMISE DRIVE DESIGNS
- 08/03/2010 - Ensuring accurate feel to Power Steering
- 12/01/2010 - Iron Bird with lightest touch
- 16/10/2009 - Sensor hones in on sharp operators
- 03/09/2009 - Testing time for business Jet
- 10/08/2009 - Non-contact torque sensor now mounts in moments
- 09/06/2009 - SAWs: A Cutting edge technology from Sensor Technology
- 23/01/2009 - Torque improvement for handling accuracy
- 03/11/2008 - Servo research points the way to improved dynamics
- 29/08/2008 - Sensor Technologys' TorqSense shows it's safer to belt up than previously thought
- 30/07/2008 - Nuclear engineers avoid contact with Sensor Technology
- 27/05/2008 - The Future of Green Cars lies in Sophisticated Testing
- 11/03/2008 - When two is better than one
- 19/12/2007 - Regen Drive turns laundry green
- 19/10/2007 - BIG PUSH TO RECYCLE PLASTIC
- 10/08/2007 - UAV takes fast track to altitude