State-of-the-art mixing system maximises anaerobic digestion
25 June 2010
Converting organic waste material into re-usable energy is an important part of the governments overall strategy for achieving targets for zero food and packaging into landfill by 2015.
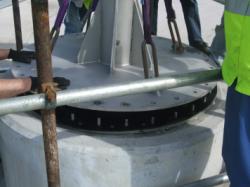
The main objectives:
The main design remit for these mixing systems was to provide 94%+ active volume mixing within the two sizes of digester proposed. Afan STW digesters required a working volume of 4300m³ with geometry of 17.8m deep x 17.2m Ø; the Cardiff digesters required 6500m³ with geometry of 20.2m deep x 20.2m Ø; while all digesters were to be new build and constructed from concrete.
The feed to these digesters is hydrolysed sludge from the Cambi process and expected to be fed into at a minimum of 10% DSC (Dried Solid Content). The requirements set by Welsh Water and by contractors Imtech Process, was to achieve a homogenous mix of the resulting digestate with a minimum of 94% active volume. System Mix and Vaughan; using CFD (Computational Fluid Dynamics) analysis, developed the design and provided detailed data to all parties showing that the mixing systems offered would achieve this requirement and furthermore, backed this up with a 10 year process warranty.
Part of the design solution required by Welsh Water and contractors, Imtech Process, was to have the internal mixing system in a format that would allow the installation and removal of mixing nozzles without the need to empty a digester, stop or interrupt the digestion process nor loose gas during this operation.
A simple yet highly effective system:
The principle of the system is simple as System Mix Ltd have designed and patented the ‘Drop-In’ Mixing Lance system that has a gas sleeve that seals with the top fluid level, allowing lance assemblies to be inserted and withdrawn without loosing gas pressure. Lances are inserted through the roof of the digester and locate on docking cones permanently installed on the floor of the vessel. These docking cones locate each lance; stopping deflection and ensuring correct alignment for optimum mixing efficiency. Nozzles are strategically placed along the lance to create the Rotamix Dual Zone mixing action; lower nozzles create rotation around and across the floor area whilst high level nozzles accelerate upper sludge volume inducing a coriolis effect which drafts high level sludge back down to the central suction points. Sludge is drawn out through the suction point to the Vaughan Chopper pumps which are located outside the vessel at ground level. The Vaughan Chopper Pumps are at the heart of all or digester mixing systems and each lance is powered by its own Vaughan Chopper pump ensuring that there is always mixing, even when a unit is out for maintenance.
The development of these high performance mixing systems is due mainly to the inclusion of the Vaughan Chopper Pump. These robust and reliable pumps condition the sludge as it passes through the impeller cutter area and this reduces solid size as well as preventing reweave agglomeration of fibrous content. The continued conditioning of sludge enhances bio digestion as well as reducing the problems of rag mass down stream in the process.
Drop-in lance enhances process:
Using Drop-In Lance mixing systems has been a significant development in digester mixing technology, these lances allow for easy removal and installation. This facility offers users greater flexibility for future enhancements by adding advance pre-digestion process like Hydrolysed Sludge Treatment of Pasteurisation as well as increases in dry solids loading, with little disruption to the biological process. The ability to maintain internals without needing to drain and enter the vessel removes the significant cost of disposing of high volumes of sludge.
Once the design of digesters was approved by Imtech Process, System Mix engineers produced detailed 3D drawings of the systems for them to include within their design package. Construction of all 4 digesters (2 at Afan and 2 at Cardiff) were completed by Morgan Est. and Imtech on time, early April 2010 and mixing systems for each were delivered in accordance with the agreed contract dates.
System Mix supervised the installation of lances into each digester; the two digesters at Afan were installed in one day and Cardiff within two days from first lift, with an average installation time of only 4 hours per vessel.
System Mix designed and installed a similar system into digesters at Anglian Waters’ Kings Lynn STW, adding credence to designs and methodology. The Kings Lynn digestion has the most productive and efficient digester and this helped convince Welsh Water that System Mix was the right solution for these applications. These successes, in addition to the standard designs installed at other advanced digestion schemes at Cotton Valley, Great Billing, and Bran Sands and Frameworks held with Southern Water, has significantly increased the awareness of these systems. This has established System Mix as an important supplier of digester mixing technology to the Anaerobic Digestion industry, not only in municipal applications but also in the rapid growth area of Bio Waste Industry.
A summary of the benefits:
The features and benefits of System Mix are; retained digester volume and minimal settlement, with over 90% being retained during its working life, maximised solids reduction, continuous recirculation during mixing ensures full distribution and breakdown of solids, both mechanically and biologically, retained gas production is maintained to levels seen at system start without drop-off, minimal cleanout costs as the digester can be easily cleaned at minimal cost. And finally, low installation costs as all rotating equipment is externally mounted and internal equipment is easily installed.
Other Press Releases By This Company
- 01/02/2012 - Ford Motor Company improve waste handling with Vaughan Chopper Pumps
- 03/08/2010 - Superior mixing systems save significant sums
- 20/11/2009 - System Mix joins ABDA to help promote anaerobic digestion
- 30/10/2009 - Vaughan Chopper Pumps "rock" for Gibraltar
- 09/09/2009 - Better mixing maximises anaerobic digestion process
- 24/07/2009 - Maximising anaerobic digestion with reliable mixing
- 24/04/2009 - When Rag becomes a drag, the choice is a Chopper Pump