‘Spiroflow’ Big Bag Discharger – a gem of a job!
30 November 2007
Dublin, Ireland based Gem Pack Foods are well pleased with the performance of the ‘Spiroflow’ Big Bag (FIBC) Discharger
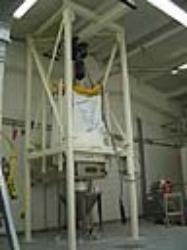
Dublin, Ireland based Gem Pack Foods are well pleased with the performance of the ‘Spiroflow’ Big Bag (FIBC) Discharger supplied to them through Irish representative Powder Process Systems. Gem Pack Foods’ Fawema packing machine has 2 feed points, one requires product be delivered at a metered feed rate and the other has it’s own auger to regulate the flow from a mass transfer system. Only one feed point can be in operation at any time. Either way, product feed to the packing head has to have a consistent flowability and has to be de-aerated within specified tolerances. To deliver the products to the packer in the condition required, Spiroflow’s suggested solution was to offer a Bulk Bag Discharger capable of connection to either one of their Flexible Screw Conveyors (which delivers product at a metered rate) or to a Vacuum Conveyor (which is a mass transfer system). Each conveying system is mobile so that change-over between the two is a quick and easy operation. In the words of the Engineering Manager at Gem Pack Foods, ‘It’s a good piece of kit!’
Gem Pack Foods Ltd are both a Contract Packer and provider of an extensive range of ‘Gem’ and ‘Gem Gourmet’ brand products - several of which are simply repacked from bulk supplies but many of which are own brand proprietary mixes. Some of their key ingredients are sugar, in various forms from granulated to fine icing grades, rice and corn flour. To keep abreast with growth in demand, Gem Pack Foods decided to have these key ingredients delivered in 1 tonne Big Bags (FIBC’s) rather than 25 kg packs to take advantage of all the well documented benefits of bulk supplies. Having dealt with Powder Process Systems previously, they were Gem Pack Foods’ natural ‘port of call’ to investigate how best to discharge this variety of products from Big Bags and to deliver each of them in the correct condition to the appropriate feed point of the packing machine.
Gem Pack Foods are discharging something in the order of 350 tonnes of sugar a week plus all the rice and corn flour they use too. These products, and mixtures thereof - together with other ingredients, are packed in to a variety of packages ranging from 3 kg in box bags down to single portion sachets. Much of their production is delivered to wholesalers and the large supermarket chains, with the remainder going for export.
As Pat Leamy, Managing Director of Powder Process Systems, confirms, “The challenge of this job was not the discharge of the products in question. For the ‘Spiroflow’ Big Bag Discharger complete with integral ‘base massagers’ and ‘bag tensioning support arms’, this is a ‘walk in the park’. However, delivering the variety of sugars and other bulk ingredients to the packing machine in the condition specified was a different story. In the end, together with Spiroflow, who liased direct with the packing machine manufacturer, we concluded that there needed to be two methods of transferring discharged product to the appropriate feed point on the packing machine. The customer accepted our proposal and the system works to his entire satisfaction”.
The ‘Spiroflow’ Bulk Bag Discharger is sited on a mezzanine floor within the main packing hall and, as a result, big bags are delivered to it by way of a pallet rather than a forklift truck. Accordingly, the discharger is furnished with its own lifting beam and travelling hoist to facilitate the easy positioning of full bags into the discharger but not before either the Flexible Screw Conveyor or Vacuum Conveyor are in position below the discharger and its umbilical cord is connected to the electrical control panel. The loops of each bag are attached to a lifting frame that ensures the bag is lifted squarely in to place. Once in place, bags sit on a substantial support dish whilst being stretched vertically by the compression springs within the side arms that support the lifting frame used to raise the bag.
The support dish houses the ‘base massagers’ that can be operated manually in the event of product being reluctant to discharge from a compacted or otherwise difficult bag. The aperture in the support dish, through which the outlet spout of the bag passes, is surrounded by an elastic membrane that makes a seal with the base of the bag - even when the massagers are in operation. Below the support dish, a containment cabinet houses a spigot which leads directly to the inlet of whichever conveyor is in position below. The neck of the big bag can be sealed to this spigot before the liner of the bag is untied. This ensures the dust-free transfer of the product into the conveyor and no contamination of the product from the outside of the bag or the operator.
The hopper that feeds the Flexible Screw Conveyor is complete with an agitator to ensure a consistent flow of product into the screw and hence into the packing machine. The conveyor is 3 metres long and raises product about a metre into a check sieve directly above one of the inlets of the packing machine.
The vacuum system collection hopper needs no agitator. The conveying distance is 6 metres and raises product to a height of 3 metres into the collection cyclone and then on into the packer by way of a rotary valve.
To learn more about ‘Spiroflow’ Big Bag Dischargers, Flexible Screw Conveyors, Vacuum Conveyors and their ranges of Aero-Mechanical Conveyors and Big Bag Fillers too, visit their web site at www.spiroflow.com or call them on +44 (0)1200 422525 to discuss your specific requirements.
Other Press Releases By This Company
- 14/10/2015 - Spiroflow's conveying solutions go on the road to Dubai
- 08/09/2015 - Spiroflow Will Unveil New Flexible Conveying System At Ppma - Ppma, Nec Birmingham, September 29-october 1, Stand G36
- 07/07/2015 - Spiroflow acquires food control solutions
- 12/02/2015 - New Technology Centre brings superior testing to spiroflow
- 03/10/2014 - Spiroflow's Robust Handling Equipment Built to Survive Stormy Seas
- 30/09/2014 - Spiroflow Takes New Angle with Equipment to Tackle Dust
- 30/09/2014 - Spiroflow Unveils New Bin Activator for Difficult Materials
- 30/09/2014 - Spiroflow Targets UK Ingredients Sector with New CTE Bulk Bag Filler
- 30/09/2014 - Safe Handling of Biomass Materials with Spiroflow
- 09/01/2013 - Spiroflow conveyors – fit as a Butcher’s dog!
- 03/07/2012 - Preview of Spiroflow Ltd’s participation in the PPMA 2012 Exhibition at the NEC, Birmingham, UK, September 25-27, 2012.
- 13/06/2012 - ‘Spiroflow’ Aero-Mechanical Conveyors – sweet success in Africa!
- 23/02/2012 - ‘Spiroflow’ Bulk Bag Filler – helping to make money from waste.
- 02/11/2011 - NEW Tilting Mobile Flexible Screw Conveyor from Spiroflow
- 12/07/2011 - Spiroflow Powder Handling & Processing Systems – Stand G16
- 29/03/2011 - New ‘Rise and Fall’ Bulk Bag Filler from Spiroflow
- 14/02/2011 - Sometimes life has to be a Drag!
- 18/12/2010 - Spiroflow joins the club at Liverpool biscuit factory
- 22/07/2010 - Bag to the future!
- 22/07/2010 - Spiroflow Ltd in joint venture with Horizon Systems Inc.
- 16/06/2010 - Spiroflow acquires Dynamet Inc.
- 16/03/2010 - United Utilities treats water to PAC Dosing System
- 17/02/2010 - Aero Mechanical Conveyor does sterling job for US coffee blender
- 02/02/2010 - Spiroflow dip dabs Tangerine Confectionery
- 27/01/2010 - Spiroflow helps recycle sulphur on Alaskas' north slope oil refinery
- 21/01/2010 - Aero-Mechanical Conveyors keep Tin Oxide moving
- 22/07/2009 - Aero-Mechanical Conveyor is no Red Herring in Orkney
- 14/05/2009 - Spiroflow Aero-Mechanical Conveyor spicing it up for Pataks
- 05/12/2008 - Highest accuracy ‘Spirofil’ Big Bag Filler to Date
- 11/11/2008 - ‘Spiroflow’ Bulk Handling Equipment at Dekura
- 18/08/2008 - Spiroflow and the 'Dream Machine.'
- 09/07/2008 - Spiroflow Supply Tetley Tea with Big Bag Discharging Solution
- 30/11/2007 - ‘Spiroflow’ Bulk Bag Filling Machine at PET Processors (UK) L.L.C
- 26/11/2007 - Nothing fishy about this discharger!
- 26/11/2007 - Spiroflow system transforms output
- 23/11/2007 - A ‘Spiroflow’ Bulk Bag Discharger and Flexible Screw Conveyor
- 23/11/2007 - Spiroflow on the road to success
- 22/11/2007 - Spiroflow conveyor gives more grist to the mill!
- 22/11/2007 - Weigh, weigh the best - time and time again!
- 22/11/2007 - ‘Spiroflow’ conveyors – to cap it all!
- 22/11/2007 - Spiroflow’ Flexible Screw Conveyors – BALly good job!