How Cadbury solved the cracking Easter egg delivery problem
08 April 2024
In the UK 80-90m chocolate Easter eggs are sold during the Spring period¹ and ITN News estimates that one third of these are from Cadbury.
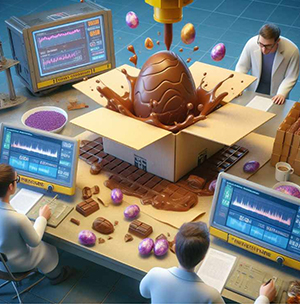
It’s no wonder that a 2023 consumer research report³ showed that 64% said that Cadbury’s was their favourite Easter egg ahead of Mars (35%), Hotel Chocolat & Thorntons (31%). So it’s vital for Cadbury that Easter eggs are delivered in one piece for that Easter Sunday thrill!
When Cadbury faced the problem of Easter eggs and other products being damaged during loading, transporting and delivery they investigated everything from production to delivery. Inspecting damaged shipping cartons and damaged products indicated that impacts and drops occurring during the shipping process would transfer force to the products inside, damaging both packaging and contents.
UNDERSTANDING IMPACT BEFORE REDESIGN
A redesign of the shipping cartons could improve the protection of the product by reducing the force being transferred to the contents during drops and impacts. But before they could start a packaging redesign the team at Cadbury needed to understand how much force would cause carton damage that would transfer to the contents and spoil the Easter egg experience. Part of the solution lay in understanding how impact forces were distributed, with a particular focus on packaging corners as these represented the smallest impact area.
After researching the issue, Cadbury decided that pressure mapping would be the best solution to measure the forces of a typical drop. This not only gave them the detailed mapping but could also provide recordings of the displays showing exactly how the force is distributed as it impacts the ground or other objects.
HIGH-TECH SENSOR MEASURES IMPACT FORCES
Interface Force was invited to visit the Birmingham factory to test this preferred solution with Interface’s supplied XSensor pressure mapping system. The sensor required for this test would need a fast sampling rate, high spatial resolution and as the force involved was not known at this point, a high-pressure measurement range. The XSensor IX510:60.60.10 sensor was selected by the Interface Force team as its 3,600 sensor points at 2.54mm spatial resolution would offer the detail needed.
Linked to the XSensor’s Pro software, live viewing and recording of the impact event was available together with measurement of the impact area, average and peak pressure being recorded with output available to be reviewed in video format (AVI) or by focusing on specific points and analysing single frame images (JPG, PNG). Cadbury could also export the full analysis into other software packages of detailed offline analysis and linking to CAD systems for eventual design to reduce and hopefully eliminate breakages cased during shipment.
PUTTING THE PACKAGING TO THE TEST: IMPACT TESTING FOR OPTIMAL DESIGN
During testing the various sizes of shipping cartons were ‘dropped’ onto the sensor mat from a height of one metre to emulate serious shipping problems. Data on the impact force and distribution was recorded and analysed and changes made to the shipping cartons. The process was then repeated to further modify design creating improved force distribution and lower impact forces.
The end result? Happy children (and adults!) on Easter Sunday received the perfect Cadbury Easter egg! When there’s an estimated 21.4 million people consuming Cadbury products² – this delivers a really happy Easter!
Happy Easter from everyone at Interface Force – enjoy your Cadbury Easter eggs.
Other Press Releases By This Company
- 26/06/2024 - Experience precision:
- 23/05/2024 - Engineering & Manufacturing 2024 / Smart Factory Expo
- 23/02/2024 - The new remote monitoring solution form Interface Force
- 24/01/2024 - Multi-axis sensors + DAQ systems go hand in hand