Steel pipework supplier gets a taste of chocolate
29 January 2010
Jacob (UK) has supplied an extensive stainless steel modular pipework ducting system for Cadbury at Marlbrook.
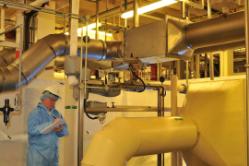
The plant operates at up to 90°c and heated air is fed to the drying tower using 300mm diameter Jacob (UK) modular ducting manufactured in stainless steel and clad with insulation material to conserve heat and protect employees from accidental contact with the hot ducting. The plant uses hot air to extract moisture from the ingredients as part of the process to produce chocolate crumb.
Jacobs' modular stainless steel ducting is again used on the extraction side of the plant to feed the used air through a filtration system to remove particles and remove the exhaust air via a noise attenuator to the atmosphere. The 400mm diameter ducting has a manually adjusted throttle valve on the exit from the filter to balance the airflow across the system.
Cadburys' Len Eades;
“By using modular stainless steel pipework supplied by Jacob, we are able to quickly disassemble the ducting when the plant is due for cleaning or routine maintenance, saving considerable time and cost.”
The factory at Marlbrook has 11 chocolate crumb manufacturing lines, which together process 180 million litres of fresh milk, 56,000 tonnes of sugar and 13,000 tonnes of cocoa liquor each year. The fully automated plant runs 24 hours per day, 365 days per year. On a scheduled basis, one chocolate crumb manufacturing machine is taken out of service for routine maintenance and a deep clean. This is where using Jacobs' modular stainless steel ducting has real advantages for Cadbury.
Every Jacob pipe section has a machine-lipped end, which when fitted with a specially designed “U” shaped gasket manufactured from Keltan (EPDM) and a removable connector, a 3-bar overpressure certified connection is created. This has the advantage of providing excellent conductivity whilst giving the added benefit of being ATEX compliant.
The thin-walled ducting sections are easily dismantled and re-connected using the Quick-Connect pull-ring system designed and manufactured by Jacob. Air movement within a Jacob pipeline is enhanced with the smooth-pressed bends, which assist airflow with the minimum of resistance. Standard accessories include inspection doors, visualisation ducts, diverters, product-control and air-control valves, all manufactured to high tolerances.
Despite being one of the largest air handling systems of its type used for confectionery production, the majority of the Jacob ducting and pipework is located out of sight, high in the ceiling ducts but accessible for inspection and maintenance. With pipework diameters from 60mm to 800mm and a comprehensive range of forks, bends, T pieces, valves and distributors, Jacob modular pipework is ideal for creating an efficient and flexible system, one which can adapt to changing requirements.
Jacob (UK) Director, John West;
“By working closely with specialist installers Jex Engineering and by using our stainless steel modular pipework, Cadbury has been able to improve efficiency by reducing the downtime required for maintenance and cleaning operations, whilst using the advantage of modular design to optimise plant layout.
Other Press Releases By This Company
- 09/11/2021 - The new horizontal cyclone from JACOB Pipework Systems, for reliable particle separation
- 03/11/2020 - More safety for your goods – Jacob detectable-design line
- 24/02/2020 - A new cutting system sets the pace in production at JACOB
- 23/04/2014 - New JACOB product catalogue – perfection in connection
- 09/05/2013 - New products – higher standards
- 30/01/2013 - Jacob debut new modular pipework products at Maintain
- 21/06/2012 - New rotary valves from Jacob UK
- 21/06/2012 - Hi-speed, fast acting valves for metal detection systems
- 14/06/2012 - Golden Wonder crisps & snacks fly thanks to Jacob
- 28/09/2009 - Jacob pipes help Ricoh stay green
- 15/06/2009 - Jacob brings Smooth conductivity – inside and out
- 21/04/2009 - Easy-fit Earthing Bridge – maintains pipework conductivity