Coiled and ready for action
16 September 2013
Leading international wire industry specialist William Hughes Ltd is enjoying increasing success in a market that has the potential to offer enormous growth opportunities.
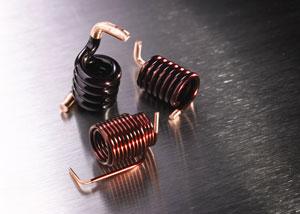
When a current passes along the specially designed conductive copper, a magnetic force is created through the middle of the coil. In the event of a current surge or spike, the magnetic force increases so that a spring is pulled to trip the main switch.
“We already have an established customer for this product in the UK – a leading manufacturer of circuit breakers and switchgear – and we are now hoping to attract another customer, this time a European giant in power technology that is in the process of setting up a new factory near our recently established Bulgarian manufacturing facility,” says the company’s managing director Max Hughes.
According to Mr Hughes, should the company be successful then part of its production for copper coils will be transferred from its UK headquarters in Stalbridge, Dorset to Bulgaria.
At present there are already a huge number of varieties of copper coils being manufactured by William Hughes. A small change to the copper coil can affect the magnetic force produced to suit different currents, making it a very efficient mechanism as there is no need to have different designs of any other standard parts.
The copper coils are manufactured on standard Japanese-built CNC machines that have been subjected to extensive modification by William Hughes’ engineers (including the manufacture of special tooling) to suit the products. The automated machines are fed with 3mm diameter copper wire that is coated with enamel.
The coating is stripped from each end to reveal the conductive copper before coiling operations take place. Bends can then be created at either end to suit mating components before the part is trimmed to length. All operations are completed in a single set-up.
The copper coils usually require high levels of dimensional accuracy from one end to the other,” explains Mr Hughes. “This is to ensure that assembly is as efficient as possible and to make it easy to change from one product to another.”
At present the company is shipping around 50,000 copper coils a week, although at peak times of production this can extend as high as 100,000 coils a week.
“Flexibility of manufacture is one of our key differentiators,” says Mr Hughes, “along with state-of-the-art machinery and the ability to provide multi-drop deliveries in line with the requirements of our customers.”
Other Press Releases By This Company
- 17/05/2024 - William Hughes expands bus bar capabilities, knowledge and capacity to cater for growing market demand
- 30/08/2023 - Significant investment keeps automotive supply chain agile and just-in-time
- 27/04/2023 - Over-moulded Lumbar Structure
- 10/01/2023 - Technology investment boosts cleanroom capabilities at William Hughes
- 09/06/2022 - William Hughes is welded to success
- 13/01/2022 - New tech, new capacity & new capabilities at William Hughes
- 09/08/2021 - Insulated bus bars formed without coating damage thanks to new approach to bending
- 03/12/2020 - William Hughes goes solar with Low Carbon Dorset - saving energy costs and reducing its carbon footprint
- 12/08/2020 - Springing into action saves the day for automotive tier one
- 19/12/2019 - William Hughes boxes clever with spot welded assembly for storage tray
- 19/11/2019 - Test Point Beads Provide a Fast and Flexible Way to Insulate and Support Components on Printed Circuit Boards
- 13/08/2019 - William Hughes can now offer Electrophoretic Painting for the protection for metal parts
- 08/07/2019 - William Hughes introduces metrology services for high precision manufacturing following the acquisition of JK Metrology
- 14/03/2019 - Salt spray testing keeps a check on corrosion-resistance at William Hughes
- 25/10/2018 - Secondary processes and finishes for springs and wire components
- 27/09/2018 - Passivation explained and demonstrated
- 31/05/2018 - William Hughes uses testing to guarantee components meet endurance requirements
- 12/12/2017 - William Hughes vacuum formed trays help protect valuable parts during storage and transportation
- 11/10/2017 - William Hughes expands European operations with the acquisition of Nosag Polska Sp. z o.o. from the DEFTA Group
- 14/09/2017 - William Hughes meets new challenges for high performance spring in critical aerospace application
- 07/08/2017 - William Hughes takes the stress out of spring specification
- 22/03/2017 - Critical components cleaned to the most demanding quality standards, approvals and specifications
- 17/02/2017 - Ultrasonic cleaning comes to Southern Manufacturing & Electronics
- 13/12/2016 - William Hughes shares spring making secrets on youtube
- 12/10/2016 - William Hughes invests £1/4 million in latest welding technology to meet growing demand for automotive seat frames
- 29/06/2016 - William Hughes apprentice programme provides young people with engineering career opportunities
- 06/06/2016 - Latest 3D measurement scanner from William Hughes
- 18/02/2016 - Clean bill of health for William Hughes
- 18/01/2016 - Specialist springs from William Hughes help improve car comfort and safety
- 11/04/2014 - William Hughes celebrates 10 years of success in Bulgaria
- 21/01/2014 - William Hughes is sole supplier of specialist compression springs to Eaton Fluid Power in Havant
- 25/10/2013 - William Hughes adds strength and versatility to its wire components with new overmoulding capability
- 08/08/2013 - Wire-form & Spring specialist expands services portfolio
- 28/06/2013 - William Hughes continues to grow its manufacturing facilities in Bulgaria
- 11/02/2013 - Passivation Plant reduces lead time for spring and bent wire forming
- 30/01/2013 - Plasma Welding expertise at William Hughes
- 18/01/2013 - Bent Wire from William Hughes gets you on the move
- 20/12/2012 - William Hughes Spring Technology at the heart of Deltex Blood Flow Monitor
- 07/12/2012 - Speedy wire solution to rear car seat frame challenge
- 02/11/2012 - Improved Spiral Springs from William Hughes
- 05/09/2012 - Need double torsion springs? No problem for William Hughes
- 03/09/2012 - William Hughes achieves NADCAP accreditation
- 16/07/2012 - Hughes expands Compression and Torsion Spring ranges