What are the top digital trends for electronics manufacturing?
14 June 2021
With artificial intelligence (AI) already a firm fixture in our smartphones, fitness trackers and smart assistants, it was really only a matter of time before we would start to see digital tools and technologies finding their way into the UK electronics manufacturing environment.
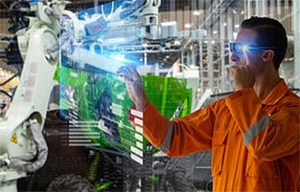
Over the past year though, the events of COVID-19 have forced many manufacturers to rethink how they can shore up their supply chains, make more effective real-time decisions and deliver an even better customer experience.
So what digital innovations look set to be firm fixtures in the factories of the future?
Predictive maintenance
While breakdowns of critical equipment are normal occurrences in the manufacturing industry, the effects can be hugely costly to manufacturers in terms of unplanned downtimes, additional repair costs and loss of productivity.
By harnessing the power of predictive analytics tools, key data can be collected from a machine and compared against its usual pattern of operation.
Even the tiniest of changes or inconsistencies can be instantly detected so manufacturers can better understand how their systems work, how they may fail and when this is likely to happen.
And because predictive testing can also be conducted even while equipment is operational, the costs, and the consequences, of planned and unplanned downtime are massively reduced.
Additive manufacturing
3D printing has been a staple in additive manufacturing for almost four decades, so it was really only a matter of time before we would start to see the printed circuit board (PCB) and integrated circuit (IC) industries capitalising on the use of 3D printers to create “smart parts” with embedded electronics.
By integrating additive manufacturing machines within the electronics manufacturing environment, there is the ability to produce a vast array of high-end electronics all of which can be created within a single, seamless process.
US-based company Nano Dimension has already demonstrated the potential of additively manufactured electronics (AME) by using their lights-out digital manufacturing DragonFly 3D printers to print a range of next-generation PCBs.
While conventionally-produced PCBs normally require the use of a pick and place machine in order to embed certain components, 3D technology makes it possible to print up to fifty alternating layers on a single circuit.
These circuits can also be stacked and interconnected in a myriad of ways which increases component density and makes it possible to work on three dimensional surfaces. Using 3D, through-holes can also be printed in any orientation and the need for drilling, etching and electroplating is eliminated.
Digital simulation
The use of simulations, virtual reality and augmented reality offer some exciting benefits for the electronics manufacturing environment - from developing prototypes to aiding in assembly maintenance and enabling operators to visualise workflows before they adjust their production lines.
Even as far back as 2015, 3D glasses were being used as standard equipment by Volkswagen to help their logistics workers facilitate order picking.
By 2019 the company had invested in cutting-edge 3D holography which enables them to project displays three-dimensionally without the need for 3D glasses.
Digital twin technology also looks set to offer manufacturers a new level of resilience and flexibility by enabling them to create virtual versions of their products and to simulate how they will perform in the real world.
The synergy of human and machine
Much has been written about the ways in which Industry 4.0 has revolutionised the manufacturing environment, with robotics, 5G connectivity and the use of data from smart devices enabling manufacturers to connect, predict and adapt their products with even greater efficiency.
Equally though, there is also increasing recognition of the value of the “human factor” in delivering unique, memorable and sustainable customer experiences.
In 2018, the Genpact manufacturing report “Manufacturing in the Age of Instinct” predicted that the coming decade would be marked by manufacturers’ embracing servitisation, with the emphasis shifting to finding new ways to create better value for customers.
While the electronics manufacturing landscape continues to be reshaped by the power of digital technologies, big data and the Internet of Things, there is also growing interest in finding ways for humans and smart devices to work together.
With the advent of Industry 5.0, we are now beginning to see the merging of the best attributes of humans and machines - combining human insight and AI techniques to improve the manufacturing process.
Charting the uptake of digital technologies
At the start of 2020 the World Economic Forum reported that more than 70% of industrial companies were still only at the start of their digital journey, with many still struggling to create the momentum that they needed to move beyond the pilot stage.
Less than twelve months later, a poll of several hundred US manufacturers in November 2020 found that more than three-quarters expected their companies to increase investment in digital technologies in the year ahead.
Now as we reach the mid-way mark of 2021, an industry report from Accenture reveals that 77% of company executives believe their technology architecture is “critical to the overall success of their organisation.”
As the events of the global pandemic of the last twelve months have proven, agility, responsiveness and resiliency are absolutely key in an environment of disruption.
Perhaps now more than ever, the new digital age offers a way for electronics manufacturers to re envision the way they do business - from streamlining their production processes, to improving the quality of their products and delivering an even better customer experience.
Other Press Releases By This Company
- 26/07/2024 - The fall and rise of vertical farming companies
- 02/07/2024 - 7 ways agricultural drones are supporting precision farming
- 12/06/2024 - What are the pros and cons of India VS ASEAN for outsourced electronics manufacturing
- 06/06/2024 - How to ensure manufacturing precision in optical sensor technology
- 29/05/2024 - Why your EMS company needs a technology roadmap
- 09/04/2024 - The EU supply chain act is coming (eventually) are you ready?
- 21/03/2024 - Ultrasonic plastic welding: what is it and who needs it?
- 12/03/2024 - 10 ways that electronic components are changing modern tractors
- 29/02/2024 - 10 powerful reasons to manufacture electronics in Malaysia
- 06/02/2024 - Does AI boost efficiency in surface mount device production?
- 22/01/2024 - How strong is your Design & Development relationship?
- 05/01/2024 - Why 3D Optical Inspection should be standard in SMD-Production
- 07/11/2023 - A new era of outsourcing? Alternatives to traditional EMS outsourcing
- 24/10/2023 - ESCATEC Promotes Lambert Schutters to CPO to Redefine Procurement Strategy
- 09/10/2023 - The future of electronics manufacturing: a conversation with SmartRep's CEO
- 21/09/2023 - 4 crucial supply chain lessons for manufacturers revealed by Covid-19
- 15/08/2023 - 9 exciting travel technology companies revolutionising air travel
- 14/07/2023 - How OEMs can reduce Scope 1 and 2 emissions
- 04/07/2023 - What is thermal management and why should you care
- 22/06/2023 - What are the 6 steps of the Value Engineering Process for OEMs?
- 27/04/2023 - ESCATEC appoints new Chairman and Independent Director
- 27/03/2023 - ESCATEC doubles up on ESG activities
- 24/03/2023 - Turning up the volume: transforming cold chain logistics during Covid-19
- 14/03/2023 - ESCATEC to exhibit at the 2023 W3+ FAIR in Germany
- 27/01/2023 - Electronic component market review - January 2023
- 25/01/2023 - Keep data safe with robust cybersecurity and IS0 27001 certification
- 06/01/2023 - What is biometric security, and what exciting tech uses it?
- 12/12/2022 - The benefits of plastic injection moulding for electronic products
- 21/11/2022 - How to get your plastic injection moulding project right first time
- 17/10/2022 - Escatec invest in new "Innovation Hub" to support growing customer demand
- 22/09/2022 - Localisation and distributed manufacturing. Is the factory really coming home?
- 22/08/2022 - 16 exciting smart farming companies (finishing what Band Aid started)
- 05/05/2022 - JJS to ESCATEC: the past 12 months and the road ahead
- 22/04/2022 - Electronic component market review - April 2022
- 14/04/2022 - Five reasons why free issue materials could prove more costly than you think
- 31/03/2022 - From Dustbusters to GPS: technology from space exploration
- 28/03/2022 - Designing the perfect supply chain: is regionalisation the answer?
- 17/03/2022 - 7 reasons manufacturers are investing in robotics in 2022
- 14/03/2022 - Has the future of additive manufacturing just changed?
- 03/03/2022 - How the conflict in Ukraine is affecting the global supply chain
- 17/02/2022 - How retrofitting boosts the circular economy and improves efficiency
- 08/02/2022 - How the global supply chain crisis built closer OEM-EMS relationships
- 27/01/2022 - Electronic component market review - January 2022
- 20/01/2022 - Repeatable success: 8 steps of a sustainable new product development process
- 14/01/2022 - 4 Supply Chain Predictions for 2022
- 10/01/2022 - Value engineering: cutting supply chain costs not product quality
- 16/12/2021 - 7 keys to success in the new product development process
- 10/12/2021 - 5 cool things MEMS sensors are doing for you
- 02/12/2021 - Reconsidering your supply chain? How about Malaysia?
- 29/11/2021 - What is MEMS?
- 18/11/2021 - Women in manufacturing: how to build the companies of tomorrow
- 11/11/2021 - How VA/VE ‘follows the money’ to deliver more value to your customers
- 27/10/2021 - Electronic component market review - Oct 2021
- 21/10/2021 - Where have all the shipping containers gone?
- 18/10/2021 - UL certification for OEMs - what do you need to sell into the US?
- 30/09/2021 - Why outsourcing to an EMS provider can give OEMs a competitive advantage
- 23/09/2021 - Never outsourced before? The right EMS partner without the drama
- 20/09/2021 - When’s the right time to start a value engineering process?
- 10/09/2021 - Why you should sign a prenup with your electronics manufacturer
- 02/09/2021 - Being held hostage by your electronics manufacturer?
- 20/08/2021 - VA/VE: 7 tips for planning your manufacturing cost reduction strategy
- 13/08/2021 - Is industrial automation the future of the EMS factory floor?
- 05/08/2021 - Subcon 2021 is back: Here’s key information to help plan your visit
- 22/07/2021 - Manufacturing trade shows are back - and they are still worth visiting
- 15/07/2021 - Electronic component market review - July 2021
- 13/07/2021 - How to cut manufacturing costs without sacrificing quality
- 01/07/2021 - What are the 6 steps of the Value Engineering Process for OEMs?
- 24/06/2021 - The secrets to maintaining a healthy outsourcing relationship
- 16/06/2021 - Value Engineering for OEMs: 7 myths debunked!
- 03/06/2021 - Volatility in the current metals market - June 2021
- 02/06/2021 - What are the pros and cons of reshoring UK electronics manufacturing?
- 20/05/2021 - The Ever Given & the future of supply chain management
- 18/05/2021 - JJS Manufacturing Acquired by ESCATEC
- 13/05/2021 - How to have effective virtual meetings with your EMS provider
- 05/05/2021 - Value Analysis and Value Engineering (VA/VE) explained for OEMs
- 30/04/2021 - Supply chain risk management in the wake of a crisis
- 22/04/2021 - Electronic component market review April 2021
- 15/04/2021 - Incoterms: why they matter for UK electronics manufacturing
- 08/04/2021 - Is component obsolescence in electronics manufacturing inevitable?
- 08/04/2021 - How to overcome 5 key challenges of electro-mechanical assembly
- 06/04/2021 - Getting a quote from an EMS provider. What could go wrong?
- 22/03/2021 - Supply chain management: Why over-forecasting is a bad idea
- 08/03/2021 - How Brexit is affecting the UK electronics manufacturing business
- 12/02/2021 - Fast, cheap or good? Feeling trapped by the iron triangle?
- 11/02/2021 - How long should your EMS provider take to prepare a quote?
- 08/02/2021 - You've chosen your EMS provider, now what?
- 05/02/2021 - 5 strategic priorities in your hunt for an EMS provider
- 21/01/2021 - When is the right time to speak to prospective EMS providers?
- 19/01/2021 - Can UK electronics manufacturers avert the global container crisis?
- 03/12/2020 - Is postponement manufacturing the best option in a post-Covid world?
- 27/11/2020 - The latest supply chain challenges to hit Electonics Manufacturing in 2020
- 13/11/2020 - Managing global manufacturing supply chains in a post-Covid world
- 11/11/2020 - Tackling the UK's manufacturing skills gap - why we must act now
- 10/11/2020 - What types of Service Level Agreement can you have with an EMS company?
- 14/10/2020 - Electronic component market review October 2020
- 13/10/2020 - 4 things to do before you speak to an EMS provider
- 12/10/2020 - What’s in an electro-mechanical build pack (& why you need one)
- 12/10/2020 - Levering the benefits of outsourced manufacturing & supply chain ownership
- 07/10/2020 - 4 ways highly flexible contract manufacturing supports innovation
- 16/09/2020 - Bells and whistles? Additive manufacturing for PCB designs
- 14/09/2020 - Can dual sourcing or multi sourcing beat supply chain uncertainty?
- 12/08/2020 - Is the manufacturing industry ready for Generation Z?
- 05/08/2020 - Small problems? 4 challenges & opportunities in PCB development
- 03/08/2020 - How will manufacturing immortality affect the product life cycle?
- 19/07/2020 - How much have attitudes shifted towards women in engineering?
- 03/07/2020 - Why outsourcing is a strategic decision
- 02/07/2020 - Robotic process automation in the manufacturing supply chain
- 12/06/2020 - How can manufacturers ensure business continuity?
- 04/06/2020 - Should UK manufacturers expect a nationwide reshoring initiative?
- 04/06/2020 - What the manufacturing environment might look like as a result of COVID-19 in the medium term manufacturing post-COVID
- 03/06/2020 - Why planning for failure is key to successful electronic assembly
- 03/06/2020 - My journey from university student to commercial graduate
- 14/05/2020 - How to withstand disruptive change in electronics manufacturing
- 28/04/2020 - 3 ways electronics manufacturing is combating the skills gap
- 27/04/2020 - Are virtual exhibitions the answer for UK electronics manufacturers?
- 27/04/2020 - Electronic component market review April 2020
- 06/04/2020 - 5 ways to combat cyber risk in UK electronics manufacturing
- 12/03/2020 - How is COVID-19 impacting the electronics manufacturing supply chain?
- 05/03/2020 - How can digital twinning benefit electronics manufacturing?
- 28/02/2020 - Which factors matter most in your PCB supplier selection strategy?
- 25/02/2020 - Three must-see Industry 4.0 events for UK electronics manufacturers
- 17/02/2020 - Securing an engineering placement - the final steps
- 07/02/2020 - What can electronics manufacturers gain from value engineering?
- 23/01/2020 - How can PCB design engineers combat raw material supply challenges?
- 17/01/2020 - Electronic component market review January 2020
- 03/01/2020 - Five ways to ace your engineering placement application
- 19/12/2019 - Gerber or ODB++ - which is best for your PCB fabrication?
- 16/12/2019 - What will your EMS partner expect to see in your build pack?
- 09/12/2019 - How digital tools can aid your postponement manufacturing strategy
- 25/11/2019 - 8 predictions for electronics manufacturing in 2020
- 14/11/2019 - What impact could CNY 2020 have on UK electronics manufacturing?
- 07/11/2019 - Is additive manufacturing the right choice for your electronic assembly?
- 04/11/2019 - What are 5 of the biggest threats to the electronics manufacturing supply chain?
- 24/10/2019 - Electronics manufacturing market review October 2019
- 18/10/2019 - Is the Smart Factory a realistic goal for UK electronics manufacturers?
- 14/10/2019 - Can SMEs overcome the seismic shifts in UK electronics manufacturing?
- 03/10/2019 - Why are rare earth elements so crucial for electronics manufacturing?
- 27/09/2019 - Is your EMS partner up to speed with WEEE 'Open Scope'?
- 23/09/2019 - How long will it take to address the UK engineering skills gap?
- 12/09/2019 - Combating ESD: the silent assassin in electronics manufacturing
- 04/09/2019 - The rising threat of social engineering for electronics manufacturers
- 22/08/2019 - Are you prepared for changes to the Conflict Minerals Regulation?
- 15/08/2019 - How can electronics manufacturers protect against cyber attacks?
- 13/08/2019 - The 7 steps to selecting a new EMS partner
- 07/08/2019 - Unit cost or total cost of supply: which matters most for UK OEMS?
- 26/07/2019 - How is the OEM/EMS partnership evolving in electronics manufacturing?
- 26/07/2019 - Could outsourcing your electronics manufacturing be the key to growth?
- 15/07/2019 - UK Electronics manufacturing 2019 - which markets are on the up?
- 05/07/2019 - Electronics manufacturing market review July 2019
- 28/06/2019 - Which test is best for your PCBA assembly - ICT or Flying Probe?
- 27/06/2019 - The 4 things every electronics manufacturer needs to know about test
- 19/06/2019 - Is digitalisation the key to the future of electronics manufacturing?
- 12/06/2019 - Is it worth keeping your electronics manufacturing in the UK?
- 30/05/2019 - What are the key questions to ask when auditing a new EMS partner?
- 23/05/2019 - 4 ways electronics manufacturers are growing their businesses in 2019
- 22/05/2019 - JJS Manufacturing returns to Subcon 2019
- 17/05/2019 - Looking to outsource to an EMS partner? Then don't miss Subcon 2019
- 09/05/2019 - What should a New Product Introduction (NPI) report look like?
- 03/05/2019 - What key questions should your EMS partner be asking in the supplier selection process?
- 29/04/2019 - How can electronics manufacturers reduce their environmental impact?
- 26/04/2019 - 8 predictions for UK electronics manufacturing in 2019
- 11/04/2019 - Electronic component market review - April 2019
- 10/04/2019 - Which IPC-A-610 class is best for your printed circuit board assembly?
- 04/04/2019 - Degree or apprenticeship – how I combined the best of both worlds
- 22/03/2019 - The hidden materials handling costs every OEM should be aware of
- 22/03/2019 - How to attract the best new electronics manufacturing talent
- 08/03/2019 - How can OEMs ensure quality supply chain management?
- 14/02/2019 - 4 ways to instantly improve the efficiency of your PCBA production
- 08/02/2019 - Industrial placements - is a sandwich year a good idea?
- 04/02/2019 - Careers for women in engineering - dispelling the myths
- 25/01/2019 - What to expect when you outsource your electronics manufacturing
- 25/01/2019 - Electronic component market review - January 2019
- 25/01/2019 - Southern Manufacturing and Electronics Exhibition
- 10/01/2019 - Six top tips to finding the right engineering degree
- 04/01/2019 - Can your EMS partner mitigate against out-of-the-box failures?
- 21/12/2018 - Three must-see UK electronics manufacturing trade shows for 2019
- 20/12/2018 - How to avoid supply chain disruption this Chinese New Year
- 20/12/2018 - Engineering placements: how to find the scheme that’s right for you
- 28/11/2018 - Manufacturers, just how effective is your induction process?
- 12/11/2018 - 4 questions OEMs typically ask when outsourcing
- 26/10/2018 - How to measure employee engagement within manufacturing
- 22/10/2018 - What to see and do at the 2018 National Graduate Recruitment Fair
- 17/10/2018 - What next - engineering apprenticeship or university degree?
- 15/10/2018 - Electronic component market review - October 2018
- 02/10/2018 - Annual EEF fact card shows solid growth for UK manufacturing
- 21/09/2018 - The Engineering Design Show 2018 - everything you need to know
- 21/09/2018 - The no-nonsense guide to Lean Manufacturing terms
- 18/09/2018 - What do SMT component shortages mean for design and manufacturing engineers
- 14/09/2018 - Looking under the hood of multi-layer ceramic capacitors (MLCCs)
- 06/09/2018 - Why ‘riding out’ the electronic components crisis is no longer an option
- 23/08/2018 - The impact of industry regulations on your manufacturing supply chain
- 20/08/2018 - How investment in staff wellbeing impacts manufacturing productivity
- 09/08/2018 - What’s driving the global demand for electronic components?
- 03/08/2018 - How engineering placements can address the UK manufacturing skills gap
- 23/07/2018 - How do manufacturers overcome growth challenges?
- 16/07/2018 - Is there an end in sight to the electronic components crisis?
- 10/07/2018 - Electronic component market review - July 2018
- 04/07/2018 - How a site visit can help you select the best electronics manufacturer
- 22/06/2018 - How to apply for a graduate scheme in manufacturing
- 24/05/2018 - How to secure a place on an electronics manufacturing graduate scheme
- 17/05/2018 - Plan your visit to the UK sub-contract manufacturing expo Subcon 2018
- 26/04/2018 - Industry 4.0 concerns
- 23/04/2018 - 5 ideas to enhance the induction process within manufacturing
- 16/04/2018 - How to assess top talent when recruiting for key manufacturing roles
- 11/04/2018 - Why Automated Optical Inspection is a must-have for PCB production
- 11/04/2018 - Have you got your outsourcing survival kit?
- 27/03/2018 - Are ineffective e-mails causing your manufacturing teams stress?
- 22/03/2018 - Drives & Controls 2018 - Tips to Planning Your Visit
- 27/02/2018 - The vital role of solder paste printing in New Product Introduction By Richard Barratt, 22 Feb, 2018
- 23/02/2018 - The Complete Guide to Outsourcing your Electronics Manufacturing
- 09/02/2018 - Should you outsource product design to an independent contractor?
- 22/01/2018 - simple ways to motivate your electronics manufacturing staff
- 22/01/2018 - Southern Manufacturing 2018: your eight-point guide to a great show
- 16/01/2018 - Is UK manufacturing ready for the fourth industrial revolution?
- 15/01/2018 - Why you want your EMS partner to be annoying and boring
- 08/01/2018 - How to select X-ray inspection equipment for electronics manufacturing
- 14/12/2017 - 9 ways to keep up with changes in manufacturing technology
- 05/12/2017 - Is your EMS provider “the one” for you?
- 17/11/2017 - Blockchain for manufacturing: what are the opportunities?
- 10/11/2017 - 5 simple elements to guarantee outsourcing success
- 03/11/2017 - What does an OEM really gain from outsourcing their manufacturing?
- 31/10/2017 - JJS to exhibit at Advanced Engineering 2017 1&2 November, NEC, Birmingham
- 24/10/2017 - Advanced Engineering 2017 - getting the most from your visit
- 24/10/2017 - Test solutions your EMS partner should offer
- 17/10/2017 - JJS to exhibit at the Engineering Design Show 2017
- 17/10/2017 - 8 factors a CEM should know about their suppliers
- 10/10/2017 - Current Market Conditions
- 10/10/2017 - Outsourcing Product Design
- 05/10/2017 - Engineering Design Show 2017 - planning your visit