ATEX Concepts: What is BS EN 14986:2017?
24 March 2023
Even though Britain has left the European Union, there are still European laws, legislative pieces and standards that have been adopted as a British standard or as formal guidelines. One example is the European standard EN 14986:2017 which has the status of a British standard through BS EN 14986:2017.
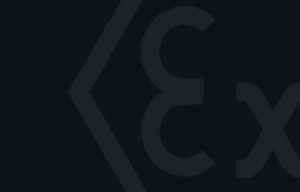
What does BS EN 14986:2017 cover?
The standard sets out the requirements for the design, construction, testing and marking of complete fan units intended for use in potentially explosive atmospheres in air containing gas, vapour, mist and/or dusts. These atmospheres may exist inside, outside or both inside and outside of the fan.
The standard is applicable to fans working in ambient atmospheres and with normal atmospheric conditions at the inlet, having:
— absolute pressures ranging from 0.8 bar to 1.1 bar,
— and temperatures ranging from −20 °C to +60 °C,
— and maximum volume fraction of 21 % oxygen content,
— and an aerodynamic energy increase of less than 25 kJ/kg.
So you don’t have to read the entire standard, we’re covering a small section in this article to assist you in ensuring the ATEX fan you purchase is designed, built, and specified in line with the legal guidelines.
BS EN 14986: 2017 Standards: Mechanical Design Criteria of Fans for Explosive Atmospheres
Section 4.4.1 of the standard describes how industrial fans should be designed to make them suitable for placement on the EU or UK market, in explosive atmospheres.
“Fans for operation in potentially explosive atmospheres shall be of rigid design.”
There’s lots of aspects that cover rigid design, and to test this fan, manufacturers should complete impact tests. “Impact testing should be undertaken on casings, supporting structures, guards, protective devices, and other external parts. Then if the deformation resulting from these tests at the most vulnerable point is so small that the moving parts of the fan do not come into contact with the casing, then the component is classed as having a rigid design.” Therefore, any fan design that’s placed on the market will have been impact tested using approved testing procedures and these results will have been sufficient to pass the tests.
Clearance between Rotating Elements and the Fan Casing
The most important safety feature of any industrial fan construction, to minimise ignition, is the clearance between the rotating elements and the fan casing.
This is clearly stated in BS EN 14986 at clause 4.4.2. “The minimum clearances between rotating parts such as the impeller and fixed parts, such as the fan casing, shall be at least 0.5% of the relevant contact diameters (diameter of the rotating part at the point where it can contact a stationary part) of the finished component, but shall not be less than 2mm in the axial or radial directions nor need be more than 13mm.” The fan manufacturer should design and construct the fan ensuring that the clearances are well maintained under all conditions covered by the intended use. Clearances may change with rotation, temperature and due to vibrations or belt drive tension. Clearances should be adhered to in application considering potential casing distortion, ductwork and pressure drops that may affect.
Fan Casing
To satisfy the mechanical design requirements specified in the standard, the fan casing should be of a substantially rigid design with leakage protection, adequate shaft seals and fully welded joints. As shaft seal leakage rate may increase over time, on request the manufacturer should provide information about the maintenance requirements for the seals. The fan should be capable of withstanding the lowest inlet pressure that can be generated by the fan itself when the inlet is closed, without causing contact between the casing and moving parts. Leakage declaration is compulsory when the internal and external zones of the fan are different.
Impellers
Impellers shall be of a rigid design and shall be able to withstand a test run at a minimum of 115 times the maximum operational rotating speed for at least 60 seconds without causing an ignition risk, i.e. the impeller shall not contact the casing. An impeller design that enables a primary stress calculation based on 2/3 of the yield stress shall be deemed to satisfy the requirements for a rigid design without testing. The security coefficient at the rotating element in our tests is a minimum of 20%. This information is recorded in the technical record.
If you’re unsure about the type of explosion proof zone you require and you have the hazardous area classification to hand, give our technical explosion proof fan experts a call or email sales@axair-fans.co.uk and we’ll talk you through the concepts, jargon and if we have the necessary information, we’ll supply a fan suitable for your application.
Other Press Releases By This Company
- 11/01/2024 - Advanced Digital Tools to Enhance Precision in Fan Specification for Fume Extraction Systems
- 15/11/2023 - BREEAM Indoor Air Quality with EC Plug Fans for Air Handling Units
- 07/09/2023 - ATEX S50 Polypropylene Fans for Fume Extraction Systems
- 04/05/2023 - Reducing Scope 2 Carbon Emissions with AHU Fan Upgrades
- 27/04/2023 - Understanding Corrosion Resistant C3, C4, C5 and CX Paint Grades
- 27/04/2023 - Energy Saving EC Forward Curved Fans for Air Curtains
- 27/03/2023 - Mechanical Ventilation with Heat Recovery (MVHR) – Basic & Quality System Differences
- 27/03/2023 - ATEX Fans Crowned Winner of The Net Innovation Award 2023
- 24/03/2023 - Zone Two ATEX Fans Designed to Equipment Category 3G
- 09/02/2023 - Corrosion Resistant Fans for Oxygen Rich Environments
- 25/01/2023 - The Complete School Fume Extraction Fan Kit
- 25/01/2023 - Centrifugal Blower Fans for Combustion Burning of Medical Waste
- 25/01/2023 - Zone One ATEX Fans for Category 2 Gas Environments
- 25/01/2023 - A Comprehensive Plug Fan Range
- 14/11/2022 - EC Fanwall Q&A for Engineers
- 24/10/2022 - The Role of the Industrial Blower Fan in Residual Waste to Energy Incineration
- 24/10/2022 - Corrosion Resistant Stainless Steel Fans – Robust & Hygienic
- 12/09/2022 - Combustible Dust Explosions in Industrial Processes
- 01/09/2022 - Exhaust Fans for Petrochemical Production in the Oil & Gas Industry
- 13/07/2022 - NIMUS Fans Improve Efficiency and Cost Reduction at UK Biomass Gas Site
- 28/06/2022 - Fans for Power Electronics Cooling
- 23/06/2022 - Replacing a Fan in a Fume Cupboard – Choosing the Right Plastic Fan
- 06/06/2022 - IIC Hydrogen Exhaust & Effective Battery Room Ventilation
- 01/06/2022 - Combustible Dust & Textile Industrial Fans
- 24/05/2022 - Ecofit Forward Curved Centrifugal Fans with AC or EC motors
- 09/05/2022 - New Launch: I-Series Backward Curved EC Plug Fans
- 05/05/2022 - Corrosive Fume Extraction Case Studies
- 21/04/2022 - Industrial Fans for Maximum Combustion in Waste Wood Renewable Energy Systems.
- 14/04/2022 - Transformer Cooling Fans
- 28/03/2022 - Air Measurement Tools for SprayBooth & Refinishing Applications
- 11/03/2022 - Industrial Fan Impellers & Fans for Spray Booth Ventilation
- 09/03/2022 - Axair Support the Development of Mobile Incineration Units
- 03/03/2022 - The advantages of multiple fans in parallel vs. a single fan in ventilation systems
- 03/12/2021 - Balanced Airflow in Heat Recovery Systems with Constant Volume Fans
- 11/08/2021 - High Performance Cooling for High Power Control Panels
- 19/07/2021 - A Fresh New Website & A Fresh New Team – How Axair Fans Has Changed
- 13/07/2021 - The Evolution of the Plug Fan
- 07/06/2021 - Extraction Fans for Indoor Swimming Pools & Chlorine Ventilation
- 18/05/2021 - Axair Partner with Buy Social Enterprise MSS-CKD
- 15/07/2020 - How to effectively protect your office spaces?
- 17/01/2020 - 5 Common Mistakes in Enclosure Cooling
- 03/01/2020 - Enclosure Cooling: Things to know about Airflow
- 14/11/2019 - Efficient Cooling Power Delivered to Rolling Stock Yard
- 15/10/2019 - The Importance of Chemical Storage Ventilation
- 24/09/2019 - 4 Ways to Cool a Cabinet
- 09/08/2019 - New Heights in Heat-Resistance: CLIBOS High Temperature Fan
- 04/07/2019 - Commercial Kitchen Extractor & Supply Air Fans
- 28/06/2019 - 4 Myths about Electrical Enclosures
- 03/05/2019 - Flexibility in Commercial Ventilation
- 11/04/2019 - Process Cooling in Factories
- 25/07/2017 - Alerting Live Enclosure Voltages with The Flash Signal Device
- 05/06/2017 - The Axair Group Launch The First ATEX IP68 Frame Axial Fan
- 24/03/2017 - Quiet fans score in laboratory environment
- 16/03/2017 - Understanding Fan Laws
- 17/02/2017 - Axair Donate to The Little Princess Trust
- 07/02/2017 - Selecting Industrial Fans For Biomass Applications
- 11/11/2016 - All About Smoke Control
- 25/10/2016 - New Product Release: Digital Electronic Speed Controller
- 06/10/2016 - Focus On Smoke, Pressurisation & Evacuation
- 09/09/2016 - Axair Fans Increase Company Portfolio
- 24/08/2016 - Getting To Know Axair Fans
- 22/07/2016 - Warehouse Ventilation | Centrifugal Roof Fans
- 02/06/2016 - Axair Fuel Fans For Efficient, Clean & Safe Biofuel Drying
- 18/04/2016 - Axair Fans UK Limited | Entering the World Of E-Commerce
- 12/04/2016 - Introduction to Mechanical Smoke Control
- 30/03/2016 - An Inland Of Revenue For AC Fans….
- 08/03/2016 - Axair Become Even More Responsive with A New Mobile Friendly Website..
- 14/01/2016 - “E” is for Energy Efficient - introducing the new E-Wheel
- 09/04/2013 - New ErP compliant Rosenberg fan
- 19/02/2013 - Rosenberg EC in-line duct fans from Axair
- 29/01/2013 - Inch blowers from Axair Fans
- 03/10/2012 - Axair offers the key to flexibility
- 06/08/2012 - Axair present new colour for enclosure cooling
- 24/02/2011 - Axairs' fans resist hazardous fumes
- 14/07/2010 - Axairs' high efficiency EC fans for installers
- 09/02/2010 - Kitchen extract fan now easy to clean